Laufstreifenversuche zeigen Potenzial von „epoxidierten Naturkautschuk“ (ENR)
Durch die Runderneuerung von Reifen wird Material eingespart, das Verfahren wird folglich zurecht als ökologisch betrachtet. Trotzdem sind damit die Möglichkeiten der Materialeinsparung noch längst nicht ausgeschöpft. Der Ersatz der konventionellen Rohstoffe Natur- und Synthesekautschuk durch sogenannten „epoxidierten Naturkautschuk“ (ENR) bringt dem Reifen nicht nur einen besseren Rollwiderstand, darüber hinaus bringt jedes Kilogramm ENR in der Laufflächenmischung auch eine CO2-Einsparung von neun bis zehn Kilogramm. Tests darüber, wie sich das Material in der Heiß- und Kaltrunderneuerung verhält, finden derzeit statt. Auch wenn die ersten Ergebnisse nicht unbedingt eindeutig waren, so zeigen sie doch, dass ENR in der Runderneuerung durchaus eine Zukunft haben kann.
Dieser Beitrag ist mit der Juni-Ausgabe der NEUE REIFENZEITUNG in unserer Runderneuerungsbeilage Retreading Special erschienen, die Abonnenten hier auch als E-Paper lesen können. Sie sind noch kein Abonnent? Das könne Sie hier ändern.
Durch die Epoxidierung von Naturkautschuk entsteht ein neues Polymer, dessen Eigenschaften denen spezieller Synthesekautschuke ähneln. Das Malaysian Rubber Board‘s Tun Abdul Razak Research Centre (TARRC) im britischen Hertford arbeitet bereits seit rund 40 Jahren mit ENRs und hatte in den 1980er Jahren gezeigt, dass das entsprechend hergestellte Material – wenn verstärkt mit Silica – überragende Rollwiderstands- und Nassgriffeigenschaften besitzt. Der erste Reifen auf ENR-Basis war dabei der limitierte Dunlop Enasave 97, noch bevor die kommerzielle Produktion des dann „Ekoprena“ genannten Materials 2013 begann.
Paul Brown, Leiter der Advanced Materials & Product Development Unit des TARRC, erläuterte kürzlich gegenüber der NEUE REIFENZEITUNG die ersten Ergebnisse, die das Material in Runderneuerungstests zeigte. Bei den ersten Tests hatte man das Material gegen Premium-Heißrunderneuerungen antreten lassen. Das gebrauchte Ekoprena im Laufstreifen bestand dabei zu 25 Molprozent aus epoxidiertem Naturkautschuk ENR, weiteren fünf Teilen Ruß und 55 Teilen des Silicats Zeosil 1165 und einer minimalen Menge an Silan als Verbindungsstoff und zur Verbesserung der Vulkanisationsabläufe. Der Vergleichsreifen bestand dabei zu 70 Prozent aus Naturkautschuk sowie 30 Prozent aus cis-BR, einem Butadien-Synthesekautschuk, sowie 53 Teilen Ruß. Die Mischungen à 30 Kilogramm wurden dabei in TARRCs Laboreinrichtungen in Hertford mit Hilfe einer „K2A Intermix“ erstellt.
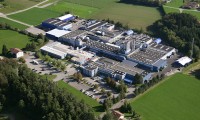
Die Mischungen und die Laufstreifen für die Ekoprena-Kaltrunderneuerung wurden bei Kraiburg Austria in Geretsberg produziert
Nach dem Mischen wurden sowohl der Ekoprena- wie auch der konventionelle Laufstreifengummi in 20 Millimeter breiten und drei Millimeter dicken Streifen auf eine abgeraute Bridgestone-Karkasse (295/80 R22,5; erste Runderneuerung) gewickelt. Laut Brown habe man eine Bridgestone-Karkasse genutzt, da sie „am passendsten für unsere Heißrunderneuerungsform“ war. Geheizt wurde dann per Dampfbetrieb ausschließlich von außen, nicht aber von innen für rund 90 Minuten. Entstanden sind dabei jeweils Reifen mit Kopien zweier Michelin-Profile, des MZA und des XDE-2. Das Profil MZA wurde dann auf der Hinterachse eines zweiachsigen Fernbusses montiert, während der XDE-2 auf der Antriebsachse einer Zugmaschine montiert wurde.
„Damit mussten die Reifen zwei verschiedenen Anforderungen genügen“, so Paul Brown von TARCC weiter. „Die Busmischung musste einen Wechsel aus Autobahn mit langen Strecken wie auch Strecken im Nahverkehr mit Fahrten von wenigen Meilen und vielem Rangieren im städtischen Umfeld bewältigen. Die Zugmaschinen hingegen wurden nahezu ausschließlich auf Autobahnen genutzt, wodurch sich eine deutlich höhere Laufleistung ergibt.“
Brown zufolge waren die ersten Testergebnisse durchaus enttäuschend. Die Verschleißwerte des Ekoprena-Reifens waren dabei deutlich höher als die des Vergleichsreifens. Bei 10.000 Meilen hatte der Ekoprena-Reifen bereits weniger als zehn Millimeter Restprofil übrig, während der Vergleichsreifen noch bei zwölf Millimetern stand. Nach den ersten 10.000 Meilen lief der Verschleiß dann allerdings bei beiden Reifen ähnlich ab. Auch bei den Reifen der Zugmaschine brachten die Tests ähnliche Befunde.
„Bei der Heißrunderneuerung war der Anfangsverschleiß von Ekoprena hoch, wobei der Verschleiß unter geringen Belastungen im Vergleich zum Referenzreifen immerhin gleich, gelegentlich sogar besser war“, so Brown. „Die Vulkanisationszeit der Reifen war lang und dabei kommt es mitunter vor, dass Ekoprena-Materialien einer größeren Reversion unterliegen als konventionelle Materialien.“ Bei der Reversion gehen durch zu viel Hitze bereits erzeugte Verknüpfungen zwischen den verschiedenen chemischen Bestandteilen wieder verloren, so dass sich die Eigenschaften des Materials negativ verändern. „Wir haben uns gefragt, inwiefern die Reversion, also das Überheizen gerade des äußeren Teils der Lauffläche des Reifens, für den hohen Anfangsverschleiß verantwortlich war. Dies wollten wir testen, indem wir es mit der Kaltrunderneuerung versuchten.“
Kaltlaufstreifen sind im Vergleich zu einem kompletten Reifen in der Form dünner und können in der Produktion von beiden Seiten geheizt werden. Das bedeutet, die Hitze zur Vulkanisation muss viel kürzere Dicken im Gummi zurücklegen, wodurch sich auch die eigentliche Heizzeit verkürzt. Außerdem werden bei der Kaltrunderneuerung auch niedrigere Temperaturen angewandt als in der Heißrunderneuerung. Da das TARCC nicht über eine Presse zur Herstellung von Kaltlaufstreifen verfügt, habe man in Kraiburg Austria einen Partner gefunden, in dessen Produktion im österreichischen Geretsberg die Laufstreifen gefertigt werden konnten. „Wir haben dabei unsere Standardmischung in einem 320-Liter-Mischer und in einem normalen dreigängigen Vorgang gemischt.“
Laut Paul Brown habe die Schwestereinrichtung des TARCC in Malaysia kürzlich mit einer ganz ähnlichen Mischung experimentiert und dabei mit Ablösungsproblemen des Laufstreifens am Stoß zu kämpfen gehabt. Um herauszufinden, ob es sich dabei um ein Problem der Herstellung des Laufstreifens oder der Produktion des Reifens handelte, hat TARCC Vergleichstests mit konventionellem und speziellem TARCC-Bindegummi gefahren. Brown zufolge habe das aber kaum Unterschiede gemacht.
Daraufhin wurden neue Lkw-Reifen geraut und dann mit konventioneller Lösung und konventionellem Bindegummi für die Runderneuerung vorbereitet. Für den Ekoprena-Reifen wurde hingegen TARCC-eigenes Bindemittel sowie der TARCC-Bindegummi genutzt. Nach konventioneller Runderneuerung im Autoklaven wurden dann die runderneuerten Reifen nach einem Standardtestverfahren (BS AU 144) getestet, wobei die Geschwindigkeit leicht erhöht war (80 km/h bei 66 und 84 Prozent Last für insgesamt sechs Stunden). Laut Brown habe TARCC mit diesem adaptierten Testverfahren in Großbritannien im Laufe der Jahre gute Erfahrungen bei der Überprüfung von Kaltlaufstreifen gemacht, wobei das Standard-EU-Verfahren eher die Schwächen der Karkasse offenbare, so Brown.
„Wir haben dann drei Testdurchläufe gefahren, ohne irgendwelche Unregelmäßigkeiten zu erfahren. Folglich haben wir dann zusammen mit Flotten einige Reifen auf die Straße gebracht“, so Brown weiter. Auch seien Labortests in Bezug auf Rollwiderstand und Nassgriff durchgeführt worden. Während der Rollwiderstand nach ISO 18614 gemessen wurde und dabei ein Rollwiderstandskoeffizient von 8,3 für den Vergleichsreifen herauskam, lag der des mit Ekoprena runderneuerten Reifens bei 7,0. „Dies ist besonders aussagekräftig, insbesondere weil beide Reifen auf identischen Karkassen entstanden waren, und zwar ohne etwaige Karkassoptimierungen.“
Der Nassgriff wurde dabei nach dem British-Standards-Institution-Verfahren BS EN 13036 auf einem stationären Pendelgerät, dem sogenannten „Pendulum Skid Tester“, und auf verschiedenen Belägen gemessen. Je höher der Messwert, umso besser der Nassgriff; während der Ekoprena-Reifen bei 75,6 landete, kam der Vergleichsreifen lediglich auf 65,6.
Für den Flottentest wurden die Reifen dann auf einem konventionellen vierachsigen Kipper montiert, wie er im Straßenbau Verwendung findet. Die letzte Achse ist dabei diejenige mit den höchsten Belastungen durch Scheuer- und Scherkräfte. Die Laufleistung auf dieser Achse ist in der Regel kaum mehr als 50.000 bis 80.000 Kilometer. Die Versuchsreifen waren lediglich 9.000 Kilometer auf der Straße, als Paul Brown gegenüber der NEUE REIFENZEITUNG von den ersten Ergebnissen berichten konnte, dennoch scheint bereits jetzt klar, dass sich der deutlich höhere Abrieb der Heißrunderneuerung bei der Ekoprena-Kaltrunderneuerung nicht replizieren ließ. Der Abnutzungsgrad der Reifen innen und außen lag für 1.000 Kilometer bei 0,332 resp. 0,371 für den Ekoprena-Reifen und 0,354 und 0,333 für den konventionellen Reifen. „Diese Zahlen liegen noch sehr dicht beieinander“, so Brown, „aber weil wir wissen, dass wir das Silica in der Ekoprena-Mischung sehr gut verteilt haben, meine ich, die richtige Heizzeit zu finden hat uns hier einige interessante Ergebnisse gebracht.“
Nimmt man die Labor- und die Straßentests nach 9.000 Kilometern zusammen, zeigt der Ekoprena-Reifen einen Vorteil beim Rollwiderstand von 15 bis 18 Prozent und beim Nassgriff von 18 bis 19 Prozent, wobei die Laufleistung – mit einer Varianz von ein bis zwei Prozent – nahezu identisch mit der des konventionell gefertigten Runderneuerten ist. Brown betont indes, dass die Aussagen zum Verschleiß lediglich auf einer einzigen Testrunde beruhen, in der allerdings auch der höhere Abrieb des zunächst Heißrunderneuerten zu finden war.
Diese ersten Ergebnisse scheinen zu bestätigen, dass sich Ekoprena durchaus als Material für die Kaltrunderneuerung eignet, liegen doch augenscheinlich gewisse Vorteile in Bezug auf Sicherheit und Umwelt vor. Die Kosten für „epoxidierten Naturkautschuk“ (ENR) würden aber vermutlich den Gebrauch im preissensiblen Segment des Marktes ausschließen. Anbieter im Premiumsegment könnten darin allerdings durchaus eine Alternative sehen. TARCC will die Tests noch für einige Zeit fortsetzen, folglich liegen noch keine konkreten Pläne für die Kommerzialisierung von Ekoprena für den Runderneuerungsmarkt vor. stephen.goodchild@tyrepress.com/ab
Schreiben Sie einen Kommentar
An Diskussionen teilnehmenHinterlassen Sie uns einen Kommentar!