Wie die Label auf (Conti-)Reifen kommen
Seit November 2012 müssen bis auf wenige Ausnahmen (Runderneuerte, Klassikreifen, Rennreifen etc.) alle innerhalb Europas in Verkehr gebrachten Pkw-, Llkw- und Lkw-Reifen mit dem sogenannten EU-Reifenlabel versehen sein. Diese Kennzeichnung soll Auskunft über deren Kraftstoffeffizienz, Nassbremsverhalten und Abrollgeräusch geben. Dafür mussten Handel und Industrie bekanntlich einiges an Aufwand stemmen, wie man beispielhaft allein schon anhand der Etikettierung der Produkte im Hause Continental ablesen kann. Denn die Frage, wie das jeweils richtige Label auf den jeweiligen Reifen kommt, ist durchaus keine triviale. Was wiederum erklärt, warum der deutsche Hersteller eigens dafür seine Logistik umgerüstet hat. Die Bluhm Systeme GmbH aus Rheinbreitbach (bei Bonn) steuerte dabei eine Etikettierungskomplettlösung bei, deren steuerungstechnisches Herz ein als extrem schnell beschriebener Industrie-PC (IPC) ist.
Warum Schnelligkeit ein Thema ist, wird sofort klar, wenn man sich vor Augen hält, dass sich bei Continental über einen einzigen Warenausgang nun rund 800 Reifen pro Stunde auf den Weg zu Kundschaft machen können. „Entscheidend ist, dass jeder Anwender die richtigen Reifen erhält – und diesen Sachverhalt auch über entsprechende Etiketten sofort erkennt“, erklärt Jörg Emrich, Projektingenieur bei der auf den Bau und Vertrieb von Kennzeichnungssystemen spezialisierten Bluhm Systeme GmbH. Der Anlagenbauer hat deshalb schon 2012 die Teleskoptransportbänder, die im Verladebereich zu den Transport-Lkw führen, modernisiert und mit entsprechenden Etikettiersystemen ausgerüstet. Dabei sei das sogenannte EU-Reifenlabel allerdings nur eine von mehreren unterschiedlichen Kennzeichnungen, die der Reifenhersteller direkt auf allen seinen Reifen platziere, so Emrich mit Blick beispielsweise auf ein eigenes Marketinglabel, das die schwarzen Rundlinge als Continental-Reifen oder eben solche einer anderen Marke des Konzerns ausweist. Abgesehen von einem hohen Durchsatz bestand bei alldem ein Problem darin, die vielen unterschiedlichen Transportsysteme mit einer einheitlichen Lösung auszustatten.
Der konstruktive Teil der Bluhm-Lösung wurde demnach so gelöst, dass über den vorhandenen Zuführbändern eine zweite Förderstrecke – gewissermaßen huckepack – gebaut wurde. In diesem Bypass befinden sich die beiden Etikettiersysteme der Rheinbreitbacher mit Namen „Alpha Quadro“ und „Legi-Air 5300“, welche die Reifen mit den entsprechenden Labels versehen. Dem hohen Datenaufkommen hat der Anlagenbauer mit einem Box-PC „Simatic IPC 627C“ von Siemens Rechnung getragen, der die gesamte Steuerungstechnik einer Etikettierstrecke übernimmt. Die Kommunikation innerhalb der Anlage läuft dabei über Profibus und zum übergeordneten SAP-System über Ethernet. Das Rückgrat des Ganzen bilden Emrich zufolge performante Intel-Core-Prozessoren, weil durch die Direktanbindung der Etikettiersysteme an Contis SAP-System bei der Zuordnung der Reifen während des Verladevorgangs rund 1,2 Millionen Barcodes überprüft werden müssen. Dabei gelte es, für vier bis fünf Reifen gleichzeitig extrem viele Parameter mit Just-in-time-Entscheidungen abzustimmen, so der Bluhm-Projektingenieur.
Die Steuerung müsse innerhalb von 200 Millisekunden überprüfen, ob der jeweilige Reifen zum Auftrag passt und welche Labels beziehungsweise welchen Aufdruck jeder einzelne Reifen erhält. „Für solch schnelle Echtzeitvorgänge sind Zykluszeiten von einer Millisekunde notwendig, die der ‚IPC 627C’ ohne Weiteres schafft“, ergänzt Emrich. Im Abstand von etwa 1,6 Metern läuft demnach schließlich etwa alle 2,5 Sekunden ein Reifen an den Etikettiersystemen vorbei, die zwar eigene Steuerungen besitzen, über digitale Ein- und Ausgänge aber an die Gesamtsteuerung angebunden sind. Die Ein- und Ausgänge innerhalb der Anlage werden über dezentrale Peripheriestationen „Simatic ET 200S“ von Siemens gebündelt und per Profibus zur Steuerung geführt. Um die Hochgeschwindigkeitsrechenprozesse im profibusfähigen Rechner nicht mit der Kommunikation zu belasten, wurde ein zusätzlicher Kommunikationsprozessor des Typs „CP 5613“ in Form einer Steckkarte in die Steuerung integriert. „Der Datenabgleich ist hier so anspruchsvoll, dass wir auf sämtliche Ressourcen zurückgreifen, die diese PC-Steuerung zu bieten hat“, sagt Emrich.
Ist ein Verladeauftrag erteilt, wird dieser eingescannt und werden die dazu gehörenden Daten aus dem SAP-System in die Anlage eingelesen. Dort verwaltet eine SQL-Datenbank sämtliche Informationen. Sobald diese Vorbereitungsarbeiten abgeschlossen sind, arbeitet die Transport- und Etikettieranlage autark, ohne dass eine Kommunikation nach außen notwendig ist. Das soll die Verfügbarkeit erhöhen und reibungslose Logistikvorgänge sichern helfen, weshalb der eingesetzte Industrie-PC auch mit einer unterbrechungsfreien Stromversorgung von Siemens ausgestattet ist. Gehört ein Reifen nicht zum Auftrag, wird er an einem Abnahmeplatz wieder aus der Linie herausgenommen, während die passenden Reifen nach dem Etikettieren über ein Transportband in den Lkw laufen. Bei alldem wird nach Aussagen des Anlagenbauers jedes Ein- und Ausgangssignal während des gesamten Transports geloggt und in eine LOG-Datei geschrieben, um nachvollziehen zu können, was im Rahmen eines Verladeauftrags passiert ist. Damit das Personal die entsprechenden Informationen auch aus der Entfernung vom Bildschirm ablesen kann, verfügt der Box-PC über einen zusätzlichen VGA-Ausgang, über den ein Standard-40-Zoll-Monitor angeschlossen werden kann.
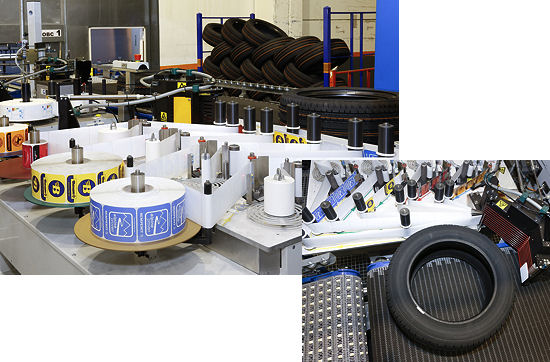
Für Continental hat Bluhm Systeme ein Etikettiersystem entwickelt und gebaut, das neben dem EU-Reifenlabel auch eines von vier unterschiedlichen Marketinglabels – entsprechend den Konzernmarken Continental, Uniroyal, Semperit und Barum – auf die Reifen klebt: Eine Positioniereinrichtung auf Basis des Servoantriebssystems „Sinamics S120“ von Siemens sorgt dafür, dass die Label mittig auf den Reifen aufgebracht werden können
Ein bzw. zwei Labels müssen letztlich am Ende des Verladevorgangs auf jedem Reifen kleben. Eines davon fällt in den Aufgabenbereich des „Alpha-Quadro“-Etikettiersystems, das eines von vier unterschiedlichen Marketinglabels – entsprechend den Marken Continental, Uniroyal, Semperit und Barum – aufbringt, während „Legi-Air 5300“ für das EU-Reifenlabel zuständig ist – oder im Exportfall für ein Exportlabel mit den reinen Reifendaten. Dabei werden per Thermotransferdruck die Daten und Eigenschaften des jeweiligen Reifens erst kurz vor dem Etikettieren aufgedruckt. „Wir waren die Ersten, die solche druckenden Etikettendruckspender auf den Markt gebracht haben“, zeigt sich der Projektingenieur Jörg Emrich sichtlich stolz. Da die Label für das Bekleben mittig zum Reifen positioniert sein müssen, sind die beiden Etikettiersysteme mit einer Hubvorrichtung für den Riemenapplikator ausgerüstet. Bezüglich des dafür notwendigen Servoantriebssystems setzt Bluhm ebenfalls auf Siemens-Technologie im Form von einem „Sinamics-S120“-Modul. Es ist dafür verantwortlich, die vertikalen Verfahrachsen beider Etikettiersysteme in die richtige Stellung zu bringen, wobei die Höhenverstellung ebenfalls über Profibus mit der IPC-Anlagensteuerung kommuniziert.
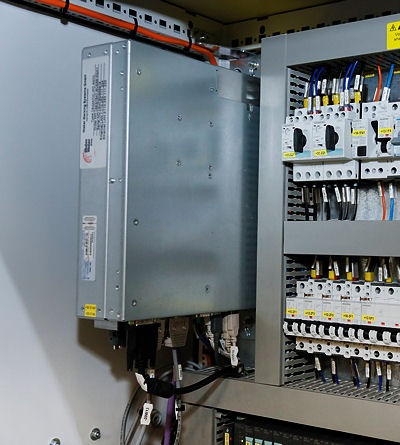
Steuerungstechnisches Herz der von Bluhm für Conti entwickelten Etikettierungskomplettlösung ist ein als extrem schnell beschriebener Industrie-PC vom Typ „Simatic IPC 627C“
„Wir schätzen hier ganz besonders die Systemdurchgängigkeit der Automatisierung, wie Siemens sie im Rahmen von ‚Totally Integrated Automation’ (TIA) verfolgt“, betont Emrich. Während nun ein einziger Industrierechner in Verbindung mit den flexiblen neuen Etikettierstationen vollautomatisch die richtigen Label auf den Reifen aufbringe, hätten früher dafür „einige Dutzend Leute schweißtreibende und mühevolle Detailarbeit leisten“ müssen, meint er. Für ihn hat das Projekt bei Continental zudem so etwas wie Vorbildcharakter: Während die Europäische Union eine der ersten Regionen mit einem eigenen „Qualitätslabel“ für Reifen sei, werde in vielen anderen Ländern schließlich an ähnlichen Richtlinien bzw. Regularien gearbeitet. „Sobald diese in der Realisierungsphase angekommen sind, haben wir bereits eine ausgereifte und praxiserprobte Komplettlösung anzubieten“, erklärt der Bluhm-Projektingenieur. cm
Schreiben Sie einen Kommentar
An Diskussionen teilnehmenHinterlassen Sie uns einen Kommentar!